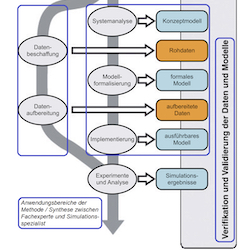
Effiziente Produktionssimulation – Eine Methode zur softwaregestützten Zusammenarbeit von Produktions- und Simulationsexperten
Produktionssimulationen sind u. a. aufgrund des Wissenstransfers zwischen dem Domänenexperten und dem Simulationsspezialisten mit einem erheblichen Aufwand verbunden. Für kleine und mittlere Unternehmen stellt dies oftmals eine wirtschaftliche Hürde bei der Nutzung der Simulation dar. In diesem Beitrag wird eine Methode für eine softwaregestützte Zusammenarbeit des Produktionsexperten mit dem Simulationsspezialisten vorgestellt, die zu einer erheblichen Aufwandsreduzierung führt. Damit können die Vorteile der Simulation bereits bei geringen Optimierungspotenzialen wirtschaftlich genutzt werden.
In Folge vorherrschender Megatrends, z. B. Nachhaltigkeit, Digitalisierung, KI, Smart Factory, sieht sich die Produktion einem rasant wandelnden Umfeld ausgesetzt. Um dem Wettbewerbsdruck standhalten zu können, sind ganzheitliche Optimierungen der Produktions- und Logistikabläufe erforderlich [1].
Eine in der Praxis etablierte Möglichkeit zur ganzheitlichen Optimierung in der Produktion ist die Wertstrommethode [2]. Hierbei handelt es sich um eine statische Momentaufnahme, die mithilfe diverser Kenngrößen, wie z. B. Kundentakt, Zykluszeit, Auslastungsgrad, Bestandsreichweite und Flussgrad, den Produktionsprozess am Kundenbedarf ausrichtet und dabei Verschwendungen identifiziert [3]. Die Wertstrommethode kann auf Basis der Betrachtung von Durchschnittskenngrößen die Dynamik im Produktionsprozess nur unzureichend abbilden. Daher scheitert die Anwendung der Wertstrommethode insbesondere bei verzweigten, parallellaufenden Materialströmen und bei kurzen Zykluszeiten [4].
Um die Dynamik in der Produktion und die wechselnden Einflüsse von Mensch, Material, Maschine etc. auf den Produktionsprozess zu optimieren, hat sich der Einsatz der ereignisdiskreten Simulation (DES) bewährt [5].
Doch Simulationsstudien in der Produktion sind trotz einer Vielzahl etablierter, allgemeingültiger Simulationswerkzeuge aufwändig. Dies begründet sich insbesondere durch die aufgabenspezifische Übertragung des Fach- und Erfahrungswissens aus dem Anwendungsbereich – das sogenannte Domänenwissen des Produktionsexperten – an den Simulationsspezialisten [6]. Nur auf Basis des Wissenstransfers ist der Simulationsspezialist in der Lage ein aufgabenspezifisches Simulationsmodell in der Simulationsumgebung zu erstellen. Der mit dem Wissenstransfer verbundene Aufwand führt in der Regel dazu, dass die Simulation in der Produktion nur zur Anwendung kommt, wenn damit erhebliche wirtschaftliche Potenziale verbunden sind. Dies ist häufig in größeren Unternehmen mit mehrschichtiger Produktion und hohen Wiederholhäufigkeiten der Fall. Für kleine und mittlere Unternehmen stellt der Aufwand von Simulationsstudien eine Barriere dar [7].
Dieser Beitrag stellt eine Methode vor, wie eine softwaregestützte Synthese des Produktions- und des Simulationsexperten die Durchführung von Simulationsstudien in der Produktion beschleunigt und den Aufwand erheblich reduziert.
Methodik der softwaregestützten Synthese
Die Methodik verfolgte den Ansatz, den Domänenexperten der Produktion und den Simulationsspezialisten gleichermaßen in die Durchführungsphasen einer Simulationsstudie einzubeziehen, um so den individuellen Aufwand der Beteiligten zu minimieren.
In klassischen Simulationsstudien, gemäß dem Vorgehensmodell nach VDI 3633 [8] (Bild 1), erfolgt die Durchführung von Simulationsstudien in fünf aufeinander folgenden Phasen. Die aufgabenspezifische Systemanalyse erfordert eine enge Zusammenarbeit des Simulationsspezialisten mit dem Produktionsexperten.
Der Simulationsspezialist fasst seine Erkenntnisse anschließend in einem Konzeptmodell zusammen, welches er mit dem Produktionsexperten gemeinsam verifiziert. Da sich nur der Simulationsspezialist, und nicht der Produktionsexperte, in der Simulationsumgebung auskennt, muss er die Modellformalisierung und Implementierung in der Simulationsumgebung vornehmen. Erst das ausführbare Simulationsmodell kann dann gemeinsam mit dem Produktionsexperten verifiziert und validiert (V&V) werden.
Eine wesentliche Möglichkeit zur Aufwandsreduzierung besteht darin, dass mithilfe eines vorab erstellten Simulations-Modulbaukastens die Phasen der Systemanalyse, der Modellformalisierung und der Implementierung nicht getrennt sequenziell ablaufen (siehe blaue Umrandung Bild 1), sondern integriert und gemeinsam zwischen Produktionsexperte und Simulationsspezialist [9].
Ermöglicht wird dies durch eine vorteilhafte Arbeitsteilung im Modellierungs- und Implementierungsprozess, durch den die beiden Experten ausschließlich auf ihr bereits vorhandenes Wissen und verfügbare Ressourcen zurückgreifen müssen, ohne sich zuvor intensiv in die Thematik ihres Gegenübers einarbeiten zu müssen.
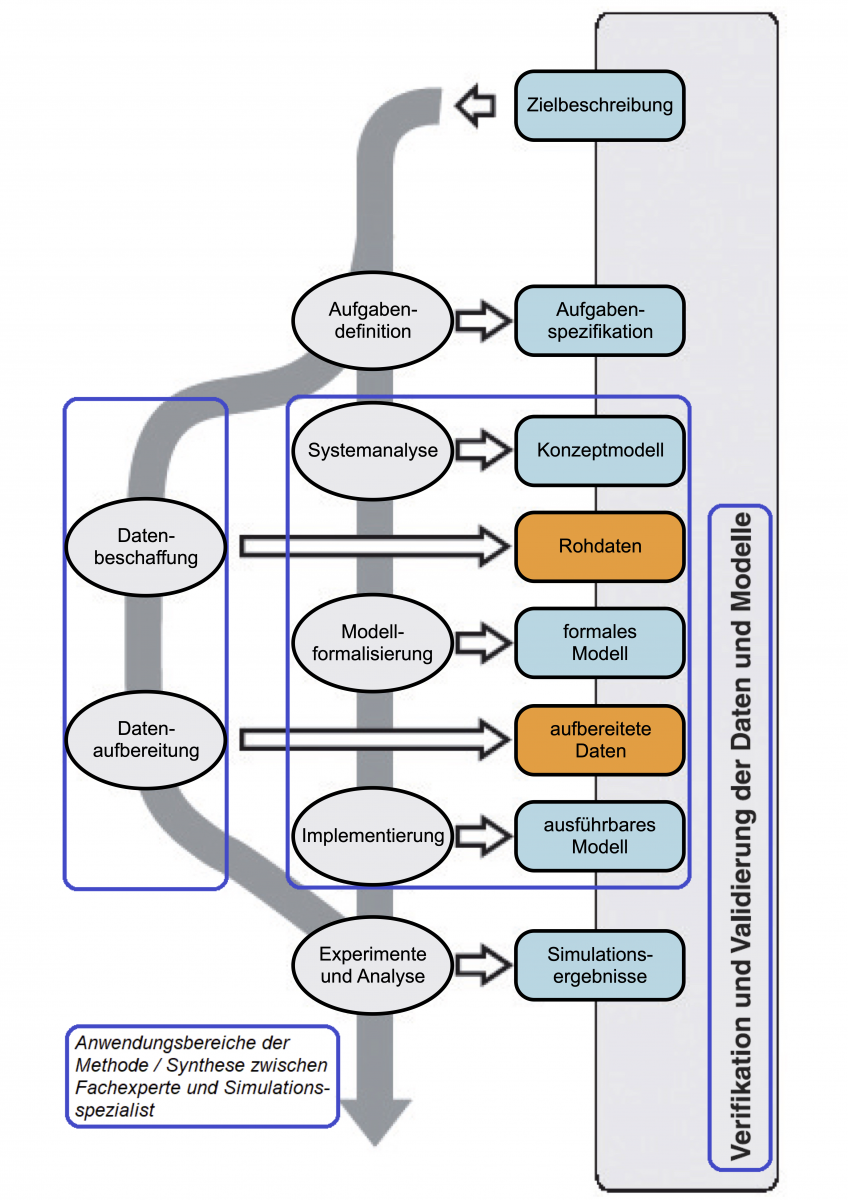
Bild 1: Vorgehensmodell der DES-Simulation nach VDI 3633 [8].
Aufbau des Simulationsmodells
In der Phase der Systemanalyse muss der Produktionsexperte den Ablauf der Produktion Schritt für Schritt dem Simulationsspezialisten erläutern. Der Simulationsspezialist erstellt dabei parallel Schritt für Schritt das Simulationsmodell, indem er aus dem vorher definierten Simulationsbausteinkasten den jeweils geeigneten Simulationsbaustein auswählt und diesen im Simulationsmodell platziert (siehe Bild 3, rot markiert).
Hierbei wird die vorab abgestimmte Aufgabenspezifikation der Simulationsstudie berücksichtigt. Zudem werden gegebenenfalls reale Prozessschritte im Modell in einem Baustein zusammengefasst oder detaillierter durch mehrere Simulationsbausteine abgebildet (Anpassung der Granularität des Simulationsmodells an die Ziele der Simulationsstudie).
Der jeweilige Simulationsbaustein hat ein spezifisches Verhalten, welches über Parameter konfiguriert und damit an den konkreten Anwendungsfall angepasst werden kann [10]. In diesem Schritt sind die Angaben von Prozess- und Rüstzeiten oder Qualitätskenngrößen und Verteilungen nicht erforderlich, da diese im Nachgang vom Produktionsexperten ermittelt (Datenbeschaffung) und in einer spezifischen Excel-Tabelle erfasst (Datenaufbereitung) werden.
Es geht in diesem Schritt ausschließlich darum, gemeinsam – zwischen Produktionsexperte und Simulationsspezialist – den geeigneten Simulationsbaustein, auf Basis der Produktionsprozessbeschreibung, auszuwählen. So muss zum Beispiel für einen Montageprozess ein Simulationsbaustein gewählt werden, der verschiedene Materialien zu einem neuen Bauteil zusammenführen kann. Auch ist ein anderer Simulationsbaustein für eine Durchlaufanlage (z. B. Glühofen) denkbar, wie bei einem Batch-Prozess (z. B. Härteofen) mit vorgegebener Beschickungsmenge.
Durch die Auswahl des geeigneten Simulationsbausteins und dessen Platzierung im Simulationsmodell sowie der Verknüpfung mit vor- oder nachgelagerten Simulationsbausteinen, entsprechend dem gegebenen Produktionsablauf, ist ein wesentlicher Implementierungsschritt ausgeführt.
Sollte das Verhalten des ausgewählten Simulationsbausteins nicht dem realen Verhalten in der Produktion entsprechen, was z. B. bei spezifischen Prozesslogiken vorkommen kann, so besteht für den Simulationsspezialisten die Möglichkeit, den Simulationsbaustein spezifisch anzupassen.
Beispiel: Eine Prüfanlage innerhalb einer verketteten Produktionslinie wiederholt, je nach Prüfergebnis, die Prüfung – was zu einer erhöhten Zykluszeit führt – oder klassifiziert das geprüfte Produkt unmittelbar als Ausschuss. Ebenso kann es vorkommen, dass ein Produkt an der Prüfanlage ankommt, welches vorab schon als fehlerhaft detektiert wurde (z. B. mit fehlendem Bauteil). In diesem Fall wird keine Prüfung an der Prüfanlage durchgeführt, sondern das Produkt wird ohne Prüfung durchgeschleust, was zu einer Reduzierung der Zykluszeit führt.
Derartige Besonderheiten treten in der Praxis immer wieder auf und verdeutlichen, wie wichtig es ist, dass die Simulationsbausteine nicht proprietär, d. h. geschlossen sind, sondern an die spezifischen Belange der Simulationsaufgabe angepasst werden können [11]. Trotz dieser Anpassungsmöglichkeit bleibt der Vorteil der schnellen, einfachen Implementierung durch die Verwendung von Simulationsbausteinen im Zuge der gemeinsamen Modellierung zwischen Produktionsexperte und Simulationsspezialist erhalten, da in dieser Phase die Besonderheiten des Produktionsschrittes nur mit einem Kommentar dokumentiert wird. Der Simulationsspezialist kann das Simulationsmodell später programmtechnisch anpassen.
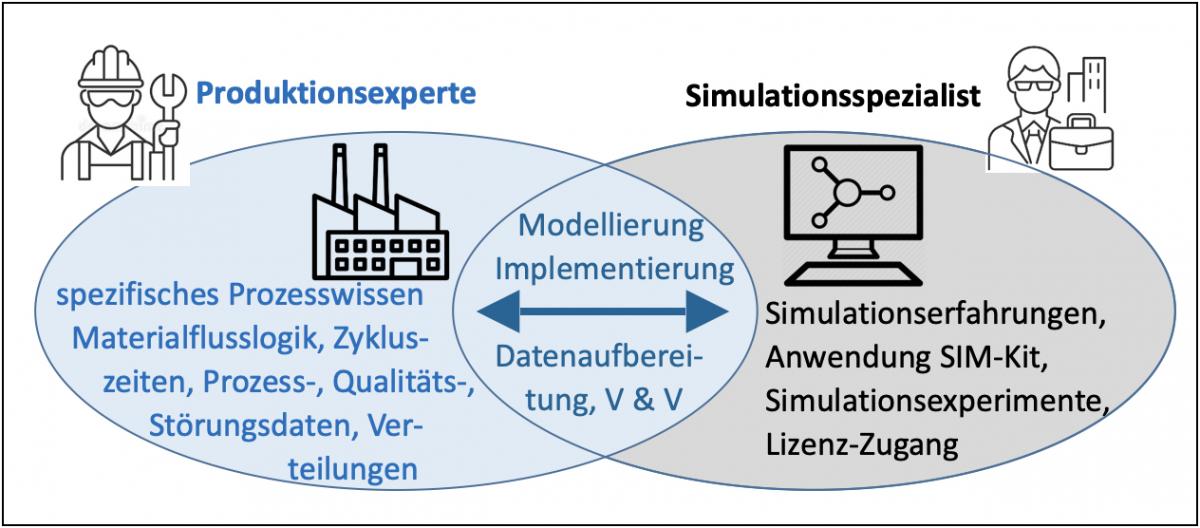
Bild 2: Konzept der softwaregestützten Synthese der Experten.
Parametrierung des Simulationsmodells
Die Parametrierung der Simulationsbausteine erfolgt aus Aufwandsgründen nicht in der gemeinsamen Modellierungszeit und nicht in der Simulationsumgebung. Dies ist zum einen darin begründet, dass die Daten der Parametrierung nahezu ausschließlich dem Produktionsexperten bekannt sind und der Simulationsspezialist hier nur einen geringen Beitrag leisten kann. Zum anderen hat der Produktionsexperte in der Regel keine Kenntnisse über die Bedienung der Simulationssoftware. Zusätzlich fehlt, meist aus Kostengründen, ein Lizenzzugriff auf die Simulationssoftware.
Daher wurde das Simulations-Toolkit so aufgebaut, dass nach der Anordnung und Verknüpfung der Simulationsbausteine in der Simulationsumgebung eine Excel-Tabelle exportiert werden kann, die alle bausteinspezifischen Parameterfelder enthält. Die Export-Tabelle kann jederzeit durch Hinzufügen von weiteren Simulationsbausteinen erweitert oder reduziert werden.
Im Anschluss an den Export der Tabelle wird diese vom Simulationsspezialisten mit dem Produktionsexperten durchgesprochen und die verschiedenen Auswahlmenüs, unter anderem für Verteilungen, erläutert. So können z. B. einem Produktionsprozess diverse Rüstprozesse in Abhängigkeit einer Auftragslosgröße oder einer Betriebszeit zugeordnet werden. Der einzelne Rüstprozess kann wiederum mit einem Werker verbunden werden. Je nach Qualifikation des Werkers können unterschiedliche Verteilungen für Rüstzeiten hinterlegt werden. Ähnliches kann für Instandhaltungen oder Qualitätsaspekte abgebildet werden.
Um den Prozess der Datenerfassung möglichst zeiteffizient zu gestalten, wurden verschiedene Eingabehilfen in der Excel-Tabelle programmiert, die anhand der getätigten Eingaben weitere Felder automatisiert ausfüllen oder mögliche Eingaben vorschlagen (Auswahlmenüs, Plausibilitätsprüfung etc.). Somit ist eine reibungslose Integration in das Simulationsmodell für einen späteren Simulationslauf gewährleistet.
Nachdem in die Excel-Tabelle alle Parameter, Verteilungen etc. vom Produktionsexperten eingetragen wurden, können diese Daten mithilfe einer Schnittstelle in das Simulationsmodell geladen werden. Anschließend kann der erste Simulationslauf durchgeführt werden, um gemeinsam, vom Produktionsexperten und Simulationsspezialisten, eine erste Verifikation und Validierung (V&V) des Modells durchzuführen. Werden hierbei Fehler im Simulationsmodell erkannt, können weitere Simulationsbausteine hinzugefügt, vorhandene angepasst oder entfernt werden.
Bei einem erneuten Export der Excel-Tabellen werden alle eingetragenen Daten exportiert. Fehlende Daten können via Excel ergänzt oder bestehende Daten vom Produktionsexperten angepasst werden. Anschließend erfolgt ein erneuter Import und eine weitere V&V des Simulationsmodells.
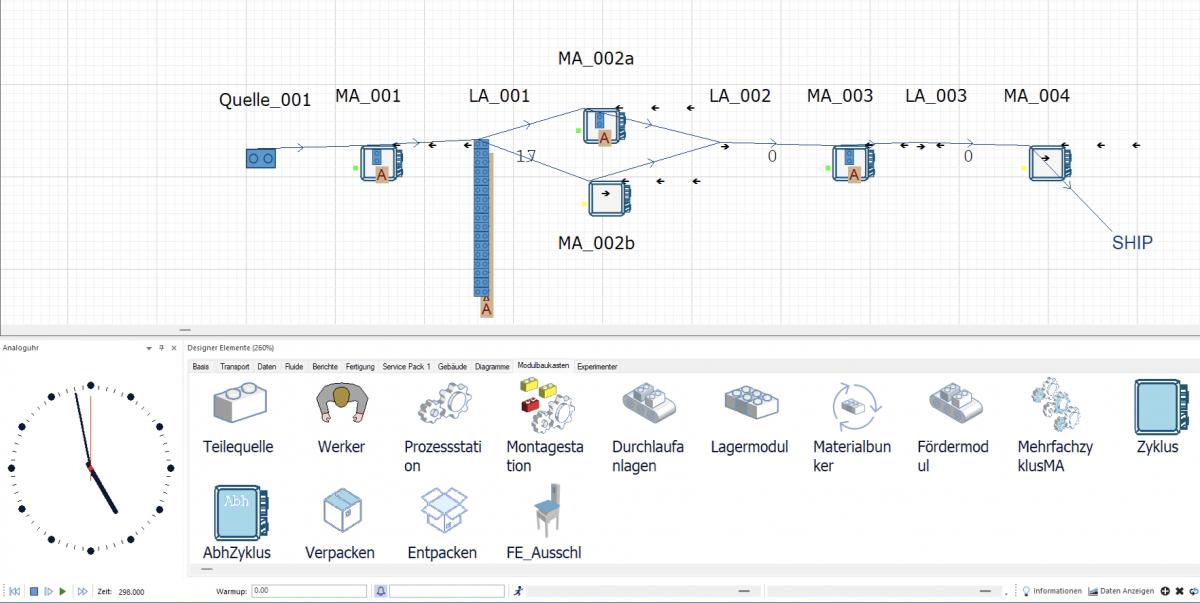
Bild 3: Simulationsbausteine und Modell in der Simulationsumgebung WITNESS.
Simulationsexperimente und KPI-Darstellungen
Entspricht das Simulationsmodell mit hinreichender Genauigkeit dem abzubildenden Produktionssystem, können anschließend die Optimierungen mithilfe von Simulationsexperimenten vollzogen werden. Auch hierzu kann die Excel-Tabelle mit unterschiedlichen Parameter-Varianten genutzt werden. Dadurch ist es möglich, vielfältige Simulationsexperimente ohne besonderen Aufwand durchzuführen.
Ist für die Experimente eine Anpassung des Simulationsmodells erforderlich, z. B. die Veränderung des Ablaufs oder eine Kapazitätserhöhung durch eine Zusatzmaschine, so kann dies im Modell angepasst werden.
Um die Resultate oder Erkenntnisse eines Simulationsexperimentes bewerten zu können, ist eine Ergebnisdarstellung in Form von Zeitverläufen, Diagrammen und Kennzahlen unerlässlich. Um auch hier den Aufwand einer Simulationsstudie in der Produktion zu reduzieren, beinhalten die Simulationsbausteine eine umfangreiche Auswertungslogik, sodass dem Simulationsspezialisten für die Darstellung der Simulationsergebnisse kein Programmieraufwand entsteht.
Eine zentrale Leistungskennzahl in der Produktion ist die Overall Equipment Effectiveness (OEE-Wert). Dieser Wert ist das Produkt aus dem Nutzungsgrad, dem Leistungsgrad und dem Qualitätsgrad einer Produktionsanlage [12]. Da der OEE-Wert sowohl für einzelne Prozessstufen bzw. Simulationsmodule als auch für die Gesamtanlage bzw. das gesamte Simulationsmodell von Interesse ist, wurde der OEE-Wert in den entsprechenden Simulationsbausteinen implementiert.
Darüber hinaus sind an einer Produktionsstation Kenngrößen wie durchschnittliche Zykluszeit, technische Ausfälle (MTTR, MTBF), Qualitätskennzahlen und Durchsatzleistungen wichtig. Hierzu gehören auch die prozentualen Anteile der Produktionsanlage bezüglich der Zustände produktiv, untätig, blockiert etc. sowie deren Darstellung über die Zeit.
Des Weiteren sind modulspezifische Kennzahlen zur Bewertung von Simulationsergebnissen von hoher Bedeutung. So sind bei der Bewertung eines Materialpuffers oder eines Lagermoduls die Auslastung über die Zeit sowie Durchschnitts- und Maximalwerte wichtig, um mögliche Optimierungen zu erkennen. Für Fördermodule sind darüber hinaus die durchschnittliche Verweilzeit und der Durchsatz wesentlich. Zusätzlich besteht im Bedarfsfall die Möglichkeit, die Ergebnisdarstellungen programmtechnisch durch den Simulationsspezialisten zu erweitern. Auch hier ist die Offenheit des Simulations-Toolkits vorteilhaft gegenüber der am Markt angebotenen proprietären Simulationstools.
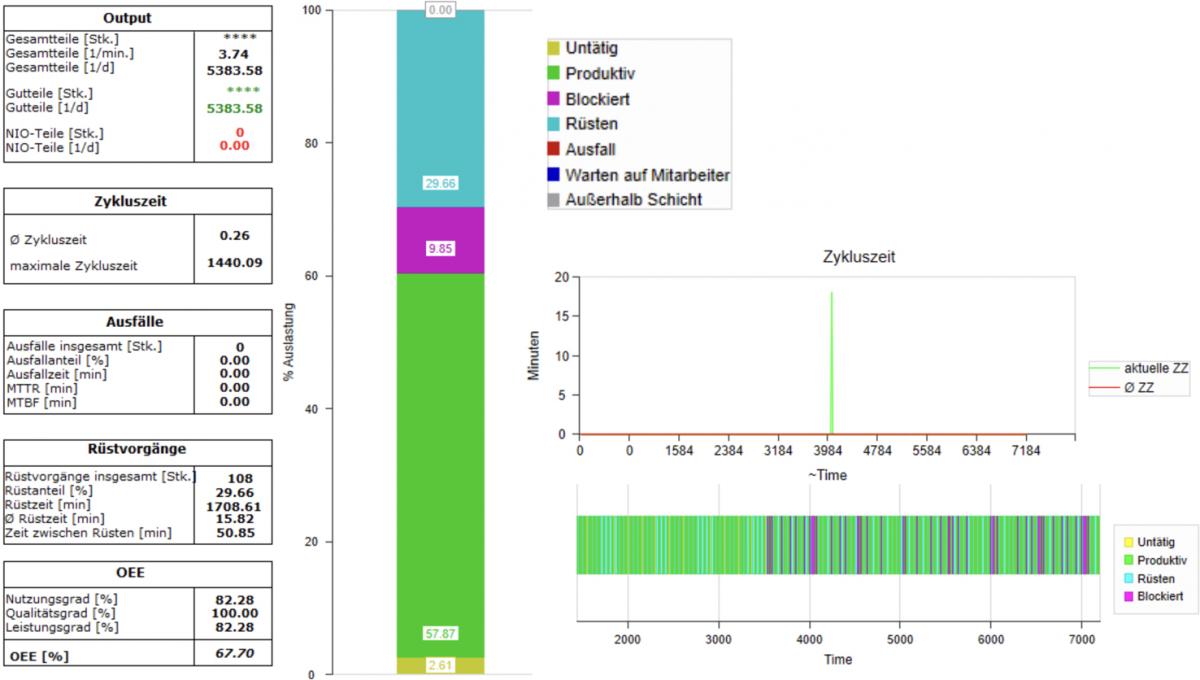
Bild 4: Beispiel-Dashboard des Simulationsbausteins Prozessstation.
Ergebnisse und Vorteile
Die programmierten Simulationsbausteine, einschließlich der KPI-basierten Ergebnisdarstellung und der Verknüpfung mit der Excel-Tabelle zur Daten- und Parametererfassung (Export, Import), können als ein Simulations-Toolkit bezeichnet werden, das eine softwaregestützte kooperative und effiziente Zusammenarbeit (Synthese) des Produktionsexperten und des Simulationsspezialisten in einer Simulationsstudie ermöglicht.
Die Phasen Systemanalyse und Modellformalisierung (gemäß VDI 3633) können anteilig mit der Implementierungsphase vorteilhaft zusammengefasst werden. Hierbei werden die Arbeitsinhalte zwischen dem Produktionsexperten und dem Simulationsspezialisten derart aufgeteilt (gemeinsame Modellierung und Implementierung sowie V&V, getrennte Parametrierung), dass die erforderlichen Interaktionen reduziert werden und der Durchführungsaufwand minimiert wird. Dadurch wird die Durchführung von Simulationsstudien in der Produktion erheblich beschleunigt. Erste Anwendungen des Simulations-Toolkits in der Praxis haben, in Abhängigkeit der Komplexität der Aufgabenstellung, eine Aufwandsreduzierung von 30-40 % ergeben.
Die wesentlichen Einsparungen entstehen in den Projektphasen Systemanalyse, Modellformalisierung und Implementierung sowie bei der Datenerfassung und -aufbereitung. Der Aufwand zur V&V sowie zur Durchführung der Simulationsexperimente reduziert sich hingegen nur geringfügig. Die zeitlichen Einsparungen nehmen bei weiteren Simulationsstudien und gleichbleibenden Akteuren zu, da die Einarbeitung in die Abläufe und die Datenerfassungstabelle für den Produktionsexperten entfallen. Somit ist die wirtschaftliche Durchführung von Simulationsstudien, auch bei geringem Optimierungspotenzial, vorteilhaft. Dies hilft insbesondere kleinen und mittleren Unternehmen, da sie damit in der Lage sind, die Simulation als Problemlösungsmöglichkeit in der Produktion effektiv zu nutzen.
Diesen Beitrag als pdf herunterladen
Schlüsselwörter:
Produktion, DES, Simulationsstudie, Optimierung, Wertstrom, Synthese der Domain- und SimulationsexpertenLiteratur:
[1] Kern, W.: Modulare Produktion. Wiesbaden 2021.
[2] Meudt, T.; Rößler, M. et. al.: Wertstromanalyse 4.0: Ganzheitliche Betrachtung von Wertstrom und Informationslogistik in der Produktion. In: ZWF Zeitschrift für wirtschaftlichen Fabrikbetrieb, Jahrgang 111 (2016) 6, S. 319-323.
[3] Erlach, K.: Der Weg zur schlanken Fabrik. Berlin Heidelberg 2020.
[4] Kaiser, J.; Urnauer, Ch.; Reif, M.; Metternich, J.: Wertstrombasierte Erstellung von Simulationsmodellen: Umsetzung dynamischer Wertstromsimulation durch ein Baukastensystem. In: ZWF Zeitschrift für wirtschaftlichen Fabrikbetrieb, Jahrgang 114 (2019) 11, S. 715-719.
[5] März, L.; Krug, W.; Rose, O.; Weigert, G.: Simulation und Optimierung in Produktion und Logistik, Praxisorientierter Leitfaden mit Fallbeispielen. Springer, Berlin, Heidelberg 2011.
[6] Gutenschwager, K.; Rabe, M.; Spiekermann, S.; Wenzel, S.: Simulation in Produktion und Logistik. Berlin Heidelberg 2017.
[7] Rudel, S.: Prozess-Simulation in KMU. Dissertation. Fakultät für Wirtschaftswissen-schaften der Universität Duisburg-Essen. Essen 2016.
[8] VDI Richtlinie 3633: Simulation von Logistik-, Materialfluss- und Produktionssystemen, Grundlagen. Blatt 1. Berlin 2014.
[9] Wincheringer, W.; Preiß, T.: Simulation von Wertstromprozessen mithilfe eines Modulbaukastens. In: Productivity: Kompetenz in Produktion und Logistik, 22 (2017). 3, S. 19-22.
[10] Sohny, T.: Referenzmodell basierend auf der Wertstrommethode zur Bewertung von automatisierten Materialflusssystemen der Produktion in der Angebotsphase. Dissertation. Fakultät für Maschinenbau, ITPL, Technische Universität Dortmund. Göttingen 2023.
[11] Wenzel, S.: Referenzmodelle für die Simulation in Produktion und Logistik. In: Society for Computer Simulation. Ghent 2000.
[12] VDI Richtlinie 2870: Ganzheitliche Produktionssysteme, Grundlagen, Einführung und Bewertung. Blatt 1. Berlin 2012.